Gear is a crucial component in various mechanical systems, from simple machinery to complex industrial applications. Understanding the types of gear and their uses can enhance efficiency and performance in your projects. This article explores different gear types, their applications, and the latest innovations. We’ll also touch on the integration of gear systems with materials like geomembrane to highlight their versatility and importance in modern engineering.
What are the main types of gear, and how do they differ?
The main types of gear include spur gears, bevel gears, helical gears, and worm gears.
- Spur Gears: These gears have straight teeth and are used to transmit motion between parallel shafts. They are known for their simplicity and efficiency but can be noisy.
- Bevel Gears: These gears have conical shapes and are used to transmit motion between intersecting shafts. They come in straight, spiral, and hypoid varieties.
- Helical Gears: These gears have teeth cut at an angle and are used for smooth and quiet operation in parallel shafts.
- Worm Gears: These consist of a worm (screw) and a worm wheel (gear) and are used to transmit motion at a 90-degree angle with high torque and speed reduction.
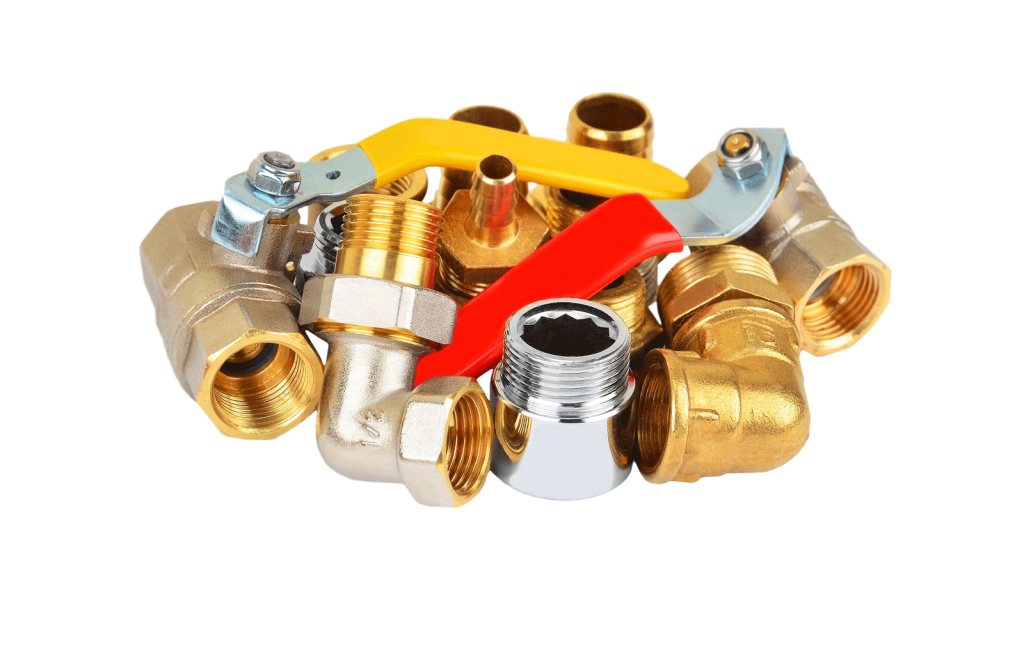
Each type has unique characteristics suited for specific applications, making it essential to choose the right gear for your needs.
How are gears used in everyday machinery?
Gears are integral to a wide range of machinery and devices:
- Automobiles: Gears in transmissions enable vehicles to shift speeds and manage power efficiently.
- Appliances: Washing machines, blenders, and other household appliances use gears to convert motor power into useful functions.
- Industrial Equipment: Gears drive conveyor belts, pumps, and other machinery in manufacturing and processing industries.
Their ability to manage and transfer mechanical power makes them indispensable in both consumer products and industrial systems.
What are the benefits of using advanced materials in gear manufacturing?
Advanced materials enhance gear performance and durability:
- High Strength: Materials like carbon fiber composites offer higher strength-to-weight ratios, improving gear performance in high-load applications.
- Corrosion Resistance: Coatings and materials such as stainless steel increase the gear’s lifespan by resisting corrosion.
- Reduced Friction: Lubricated materials and advanced composites reduce friction, leading to smoother operation and energy efficiency.
One notable material in this context is geomembrane, often used as a lining material in various applications. Though not a gear material itself, geomembranes can be found in systems that use gears, such as in water management and environmental containment projects. They help protect gear systems from environmental factors, ensuring longer operational life.
What are the latest innovations in gear technology?
Recent innovations in gear technology focus on enhancing performance and efficiency:
- Additive Manufacturing: 3D printing allows for the creation of complex gear designs that are lighter and more efficient.
- Smart Gears: Integration of sensors in gears provides real-time monitoring and diagnostics, leading to predictive maintenance.
- Advanced Coatings: New coatings reduce wear and tear, extending gear life and maintaining performance under extreme conditions.
These innovations help meet the increasing demands for precision and efficiency in modern engineering.
Gears are essential components in a wide range of machinery, from everyday appliances to complex industrial systems. Understanding the different types of gears, their applications, and the benefits of advanced materials can significantly impact performance and efficiency. Innovations such as additive manufacturing and smart gear technology continue to push the boundaries of what gears can achieve. In projects involving geomembranes, gears play a critical role in systems designed for environmental protection and management, showcasing their versatility and importance in modern engineering.