nibco butterfly valve
butterfly valve pvc
butterfly check valve
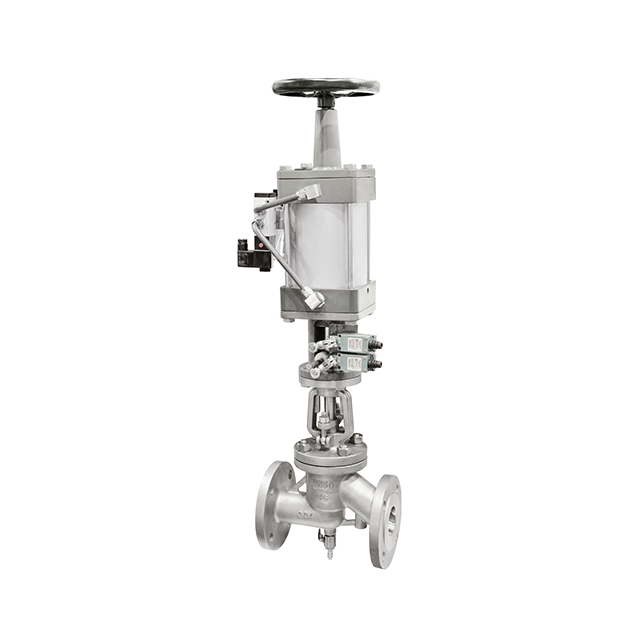
Boosting Efficiency with Pneumatic Valve Actuators: A Closer Look
March 18, 2024 by Brina
You have probably wondered how a pneumatic valve actuator works. These devices use compressed air to move a valve closure member (plug, spring, or nut) into the desired position. To work, they must be powerful enough to seat the valve closure member with enough torque, and they should be protected against external forces. The actuator must also provide enough power, both in springs and fluid power, to keep the valve in the desired position. The best actuators also provide fail positions for safety purposes.
When used in manufacturing, pneumatic valves extend the life of moving parts. This means that faulty valves can reduce the speed, accuracy, and fluidity of a machine. When functioning properly, pneumatic valves can increase the speed, accuracy, and fluidity of a process.
Table of Contents
Toggle
- How Does a Pneumatic Valve Actuator Work?
- What is a Pneumatic Valve?
How Does a Pneumatic Valve Actuator Work?
If you are curious about how a pneumatic valve actuator works, then you’ve come to the right place. This article will discuss the differences between hydraulic and pneumatic valve actuators and how they work. If you’re looking to install a pneumatic valve actuator, you’ll need to determine which type of valve is right for your needs. The difference between the two types of valve actuators is the pressure they operate at. The more pressurized a system is, the higher the pressure.
When air pressure changes, the diaphragm moves away from the valve seat. The air pressure acts against the valve plug, and this force opens the valve. Figure 6.6.7 illustrates this process graphically. For a 0.6 bar actuator, the valve will not open 50%, but at 1.1 bar, it will close to its full position. This same principle works for larger valves. The larger the diaphragm area, the higher the pressure and the more force it will generate.
Electric actuators usually have a duty cycle of 50% or less. This means that they cannot run continuously but must rest after each actuation cycle. A 50% duty cycle actuator will need at least eight seconds of recovery time before it can actuate. During this time, the positioner acts as an amplifier, modulating the supply air pressure to the actuator. A 0.6 bar valve lift would need 1.5 bar of air in the actuator’s diaphragm chamber.
What is a Pneumatic Valve?
If you aren’t familiar with the workings of a pneumatic valve, you might be wondering: what is it? Pneumatic valves use air pressure to perform their functions, much like a solenoid. Compressed air pushes against a piston or diaphragm, which actuates the valve. However, there are some things that you should know about this type of valve before you install it.
A pneumatic valve has two parts: the core and the solenoid. The core contains the solenoid coil, which is a copper wire wound around a magnetic core. The current that flows through the coil creates a magnetic field, which affects the resistance of the core. As the pressure builds up, the solenoid valve closes and opens, controlling the flow of gas or liquid. It is designed to be attracted to the magnetic field of the coil, and when the core is disconnected, a spring returns it to its original position. The other part of the valve is the stem, which connects the core to the valve body. This stem moves along with the core to actuate the valve.
A pneumatic valve comes with one to four ports and may have two to four ways. Its first port connects to an actuator, the second to an airflow tube, and the third is an outlet. Pneumatic valves may be inline, subplate, or sectional stacked. The different mounting styles and functions make it possible to choose the right valve for your specific needs. The best way to choose the right valve for the job is to understand its function and the terminology associated with it.
electric butterfly valve
manual butterfly valve