2 ball valves
sanitary ball valves
flo tite ball valves
steam ball valves
ZECO Valve Group has dozens of technical engineers who are specialized in valve technology and pipeline valve solutions and can improve the valve technical consulting services in the whole field of the petrochemical industry. With professional advanced analysis theory and technical means, ZECO combines the actual working conditions of different industries to give users the most suitable suggestions and schemes. ZECO can undertake the turnkey factory of pipeline flow transformation and pipeline valve transformation. The user is the investor of the factory and ZECO is the contractor.
ZECO International Standard Valve Manufacturer is responsible for the design, supply, and construction of pipeline flow transformation projects or pipeline valve transformation projects. After the normal trial operation and qualified acceptance, the project will be completely transferred to the user, that is, the “key” of project ownership and management right will be handed over to the user according to the contract, and the user can immediately start normal production after receiving it.
ZECO is engaged in the field of international standard valves for more than 30 years, at the same time ZECO technology chief engineer is the China valve association expert committee, the international valve standards committee member, the Shanghai fluid engineering society valve technology experts committee member, can lead ZECO technical team to provide strong technical support, can also solve the line flow and the product for the user of the incurable diseases.
Table of Contents
- Valve and Plant Service
- Valve Engineering Capabilities
- Valve Engineering Examples
- Ball Valve Design
- Ball Valve Design – Body Design
- Ball Valve Design – Ball Design
- Ball Valve Design – Seat Design
- Ball Valve Design – Bore design
- Ball Valve Design – Fire Safe Design
- Ball Valve Design – Anti-static Design
Valve and Plant Service
- Plant Engineering Support
- Air Operated Valves
- Motor Operated Valves
- Check Valve
- Safety/Relief Valves
Valve Engineering Capabilities
- Valve research and development
- Valve failure analysis
- New valve designs for demanding applications
- Valve and actuator mechanical testing
- Flow loop testing
- Qualification of valve designs to meet structural and performance specifications
- Analytical models to predict valve performance under conditions difficult/expensive to test
- Flow Testing and CFD to Determine Disc Shape Effects
- Valve/actuator design modifications
- Valve analysis per ASME and API code requirements
- Plant-wide application reviews and development of preventive maintenance programs
Valve Engineering Examples
- Analytical models to predict the performance of motor-operated, air-operated, and hydraulically operated gate, butterfly, and globe valves, safety relief valves, and check valves
- The rigorous approach to addressing flutter-induced damage of large butterfly valves
- Assessment of a large butterfly valve experiencing hydrodynamic torque fluctuations
- Flow loop testing to support model development for balanced globe valves
- CFD analyses to support model development for balanced globe valves
- A patented Sentinel gate valve to provide tight shut-off and eliminate degradation in critical nuclear power plant applications
- A tapered plug valve that eliminates taper locking of the plug under rapid hydraulic transients
- Bending moment valve testing to determine internal distortions as well as structural and performance capabilities under simulated piping loads
- Wear and fatigue models for check valves to prevent failure and prioritize maintenance
- A low-impact, gaseous cryogenic pressure relief valve with modulating pressure control for NASA’s ground support facilities
- A miniature high temperature, high pressure, low noise throttle valve for underwater propulsion systems in defense applications
Ball Valve Design
Ball Valve Design – Body Design
Ball valves are available in the following body designs.
- Single piece body design with side insert
- Two piece body design
- Three piece body design
- Fully welded body design
Ball Valve Design – Ball Design
- Floating ball design: The valve seats provide support to the ball to accommodate different temperature applications. This is the most commonly used ball design.
- Trunnion ball design: The ball is supported on the bottom and top to reduce the load on the valve seats. This design is used in high-quality valves to provide reliable sealing in both high and low-pressure applications.
Ball Valve Design – Seat Design
- Soft Seat: Ball valves are usually provided with soft seats such as PTFE, filled PTFE, Nylon, Buna-N, and Neoprene which limits the maximum working temperature and makes the valve unsuitable for abrasive service. For abrasive service applications or high integrity applications metal to metal seated ball valves can be used as described below.
- Metal to Metal Seat: For applications where elastomeric seats would be inappropriate, such as very high pressure, temperatures above 392°F, or where solid particles are present in the fluid, valves are provided with metal/metal seating, incorporating tungsten carbide coating. For high temperature service, the valves are normally fitted with extension bonnets, to ensure that the operator is located in the ambient temperature zone. Metal seated ball valves are normally used, whenever a high safety level is required, as in the HIPPS application. Seat leakage test is carried out in accordance with BS 6755 part I, rate B.
Ball Valve Design – Bore design
- Reduced bore: The bore size of these valves is smaller than the diameter of the inlet/outlet connections. Thus, there is a friction loss in the system. However, the losses are still small in comparison to other valves. Most ball valves use a reduced-bore design.
- Full bore: The bore size of these valves is the same size as the diameter of the pipe. Thus, there is no extra friction loss and they are also easy to clean. However, due to its larger diameter, the cost is slightly higher and not required for most applications, for which a standard reduced bore is sufficient.
- V-shaped bore: The bore in these valves have a V-shaped profile. Thus, a precise flow rate can be achieved by rotating the ball. A linear flow can be achieved by optimizing the profile of the V-shaped bore.
Ball Valve Design – Fire Safe Design
If a fire-safe design is required, the valve shall be qualified as “FIRE-SAFE” in accordance with one of the following specifications, ISO 10497, BS 6755-2, API 607, or API 6FA.
Ball Valve Design – Anti-static Design
When valves are provided with soft seats, their design shall ensure electric continuity between the ball and the body, by means of an anti-static device. The anti-static design ensures electrical continuity between the ball, stem and body of the valve.
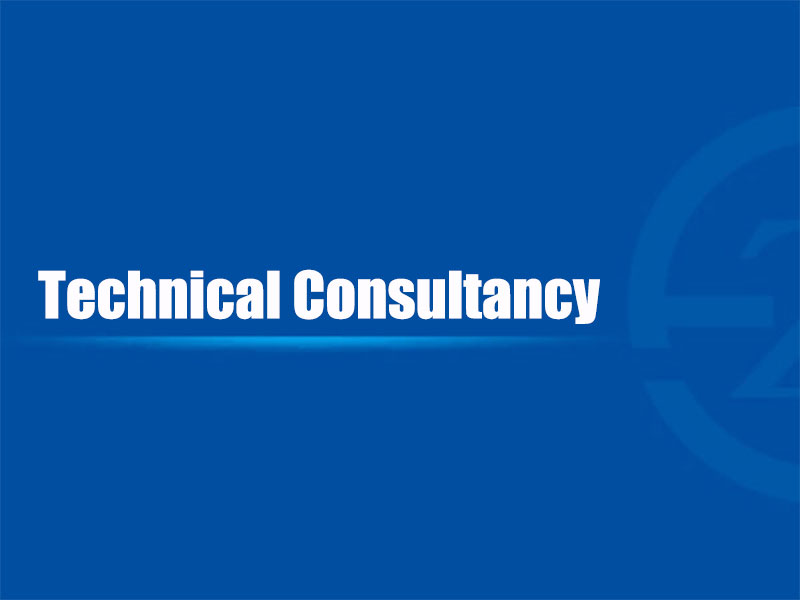